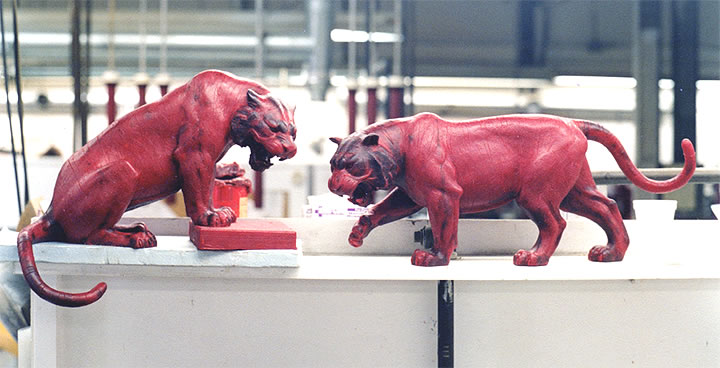
Here are some basic points for casting the lost wax method
The lost wax process consists of first making a hollow wax by painting the wax in a mold. The wax thickness is generally built up to 3/16" to 1/4" thick. Once the wax is made, seam lines from the mold making process need to be reworked, and some sculptures need to be cut and cast separately (i.e. tail). These parts are later welded back to the finished bronze.
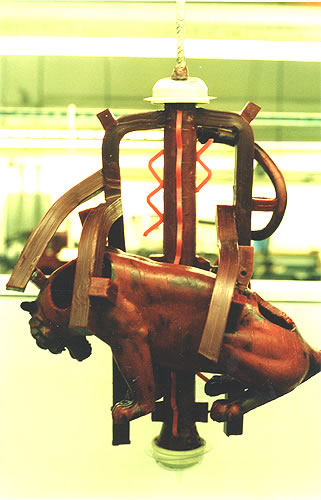
Once the wax sculpture is reworked it is attached to a series of wax gates, sprues and runners. This plumbing system provides venting and a way for the bronze to flow into the sculpture easily.
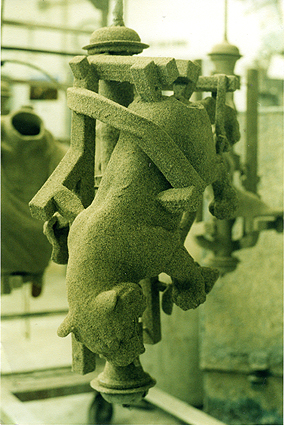
Here the wax and plumbing system is coated with layers of ceramic shell material that dry before applying the next coat (approximately 7 coats total). Once this is completed the shell with the wax inside is taken to a furnace and the wax is melted completely out, leaving the shell hollow. The ingot is heated and the molten bronze or other metal is poured into the shell, the metal taking the place of the wax.

The cast sculpture is set to cool afterwhich the shell is knocked off revealing the bronze sculpture inside. Then the process of finishing and welding the bronze begins, followed by the patina process adding colors to the metal surface.
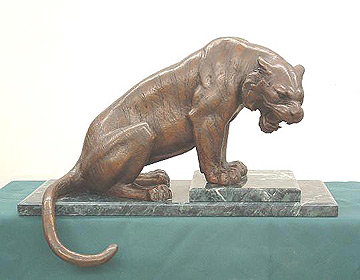
For episodes showing the complete process in detail of maquette to bronze momument go to the following page. The Sachem Daniel Nimham Sculpture is being filmed.
|